Frequently Asked Questions
If you want to learn more or book a collection, please get in touch.
What is remanufacturing?
Remanufacturing of medical devices involves inspecting, cleaning, functional testing, and packaging previously used single-use devices to ensure they meet clinical and safety standards for reuse.
This process offers sustainable and cost-effective solutions while maintaining patient safety.
This process offers sustainable and cost-effective solutions while maintaining patient safety.
How can devices labelled single use be remanufactured?
The decision to label a device as single use or reusable lies with the manufacturer:
“A device may be labeled as single-use because the manufacturer believes that it cannot be safely and reliably used more than once, or because the manufacturer chooses not to conduct the studies needed to demonstrate that the device can be labeled as reusable”
– US Government Accountability Office, 3 March 2008
Many devices are labelled single-use because the manufacturer chooses not to validate or distribute cleaning instructions to hospitals. As the legal manufacturer of all devices it remanufactures, Medsalv carries out the necessary studies and validation to ensure the safe return of each device back into the market.
“A device may be labeled as single-use because the manufacturer believes that it cannot be safely and reliably used more than once, or because the manufacturer chooses not to conduct the studies needed to demonstrate that the device can be labeled as reusable”
– US Government Accountability Office, 3 March 2008
Many devices are labelled single-use because the manufacturer chooses not to validate or distribute cleaning instructions to hospitals. As the legal manufacturer of all devices it remanufactures, Medsalv carries out the necessary studies and validation to ensure the safe return of each device back into the market.
How does Medsalv remanufacture devices to make sure they are substantially equivalent to new devices?
Collected devices undergo a thorough initial inspection, followed by cleaning and further inspections.
Every device is functionally tested to ensure it performs as intended during clinical use.
Cleaning removes bio-burden and preserves appearance before devices are appropriately disinfected.
Clean devices are sorted and undergo suitable disinfection as required.
Throughout each stage of our process, and between each step, every device goes through multiple inspections to guarantee that remanufactured devices match the quality of a new device.
Every device is functionally tested to ensure it performs as intended during clinical use.
Cleaning removes bio-burden and preserves appearance before devices are appropriately disinfected.
Clean devices are sorted and undergo suitable disinfection as required.
Throughout each stage of our process, and between each step, every device goes through multiple inspections to guarantee that remanufactured devices match the quality of a new device.
How can we tell if a device has been remanufactured by Medsalv?
All devices remanufactured by Medsalv are permanently marked with a Medsalv branded barcode or mark, in a way that cannot be removed without destroying the device. Barcodes or marks are put on the devices themselves, as opposed to the packaging.
Barcodes uniquely identify each device and allow for tracking of both remanufacturing and distribution of the devices.
This system allows Medsalv to record valuable data about the quality of devices from different manufacturers, and feed this back to your hospital.
Barcodes uniquely identify each device and allow for tracking of both remanufacturing and distribution of the devices.
This system allows Medsalv to record valuable data about the quality of devices from different manufacturers, and feed this back to your hospital.
How much can a hospital expect to save with Medsalv?
Medsalv’s remanufactured devices are sold directly to customers at up to 60% off the cost of a new device, a clear and significant saving.
Waste savings from landfills range from 80% to 100% of target devices, with end-of-life devices being recycled through other sustainable initatives.
Waste savings from landfills range from 80% to 100% of target devices, with end-of-life devices being recycled through other sustainable initatives.
What happens to devices once they can no longer be remanufactured?
Devices that fail Medsalv’s strict quality standards are broken apart into their individual materials and recycled where possible.
We are continually pursuing avenues for the reuse and recycling of end-of-life devices.
We are continually pursuing avenues for the reuse and recycling of end-of-life devices.
What ongoing input will be required by my hospital?
All devices for remanufacturing are placed into reusable Medsalv collection bags.
If your hospital is in an urban area where Medsalv has a full service established, collection bags are regularly collected and replaced with empty ones, by Medsalv staff.
In rural or regional hospitals, or those where Medsalv has not yet established a collection service, your hospital can still participate.
Simply order some reusable Medsalv bags (free of charge), and collect devices in them; place full bags in used cardboard boxes or, if you are receiving our remanufactured devices, our reusable cartons. Once you have a few boxes sealed and ready to be collected, use our online portal to notify us.
Medsalv handles the rest.
This includes providing staff education, device collection, counting, sorting, remanufacturing and re-delivery of the devices to your hospital when ordered.
If your hospital is in an urban area where Medsalv has a full service established, collection bags are regularly collected and replaced with empty ones, by Medsalv staff.
In rural or regional hospitals, or those where Medsalv has not yet established a collection service, your hospital can still participate.
Simply order some reusable Medsalv bags (free of charge), and collect devices in them; place full bags in used cardboard boxes or, if you are receiving our remanufactured devices, our reusable cartons. Once you have a few boxes sealed and ready to be collected, use our online portal to notify us.
Medsalv handles the rest.
This includes providing staff education, device collection, counting, sorting, remanufacturing and re-delivery of the devices to your hospital when ordered.
How are the collected devices transported to Medsalv? Who pays for it?
Medsalv has been designed to suit your hospital with collection points in suitable hospital areas and provides education to staff collecting devices.
Medsalv is responsible for picking up, remanufacturing, and returning devices to the facility.
Medsalv does not collect devices that are soiled, contaminated with bodily fluids, or from patients in isolation. We collaborate with each hospital to align our collection protocols and criteria with standard hospital guidelines, ensuring easy compliance.
Medsalv covers the collection costs and the returning costs, which are built into the price of returned devices.
Medsalv’s collection system meets healthcare waste requirements and uses fully reusable collection bags and containers.
Medsalv is responsible for picking up, remanufacturing, and returning devices to the facility.
Medsalv does not collect devices that are soiled, contaminated with bodily fluids, or from patients in isolation. We collaborate with each hospital to align our collection protocols and criteria with standard hospital guidelines, ensuring easy compliance.
Medsalv covers the collection costs and the returning costs, which are built into the price of returned devices.
Medsalv’s collection system meets healthcare waste requirements and uses fully reusable collection bags and containers.
Which standards do processes for non-invasive devices follow in disinfection?
Remanufacturing single-use medical devices is a manufacturing activity, governed by the Essential Principles of Safety and Performance of Medical Devices, as with any other Medical Device Manufacturing activity.
While there are no specific standards for remanufacturing, guidelines from relevant standards for disinfection of devices of similar levels of complexity are directly relevant.
While there are no specific standards for remanufacturing, guidelines from relevant standards for disinfection of devices of similar levels of complexity are directly relevant.
But I’ve seen a guideline that says Single-Use Medical Devices cannot be reused?
That's correct. A Single-Use Medical Device (or Single Patient Use device) should not be reused on another patient and must be discarded after use.
If the device meets collection criteria, it can be placed in a Medsalv collection point, if your hospital has one in place.
Remanufacturing a single-use or single-patient-use medical device does not convert it into a reusable device. Instead, it becomes a remanufactured single-use or single-patient-use device, safe for use after undergoing remanufacturing. It must be remanufactured between uses.
Remanufactured Medical devices are subject to the same regulatory requirements as original devices. Medsalv remanufactured devices are marked as remanufactured by Medsalv on the device, to ensure stringent product traceability.
A Medsalv remanufactured single-use medical device holds an ARTG (Australia) or WAND Listing (New Zealand), the same as any other single-use device.
This is a separate listing to the original device, because Medsalv becomes the Manufacturer of Record for the remanufactured device.
If the device meets collection criteria, it can be placed in a Medsalv collection point, if your hospital has one in place.
Remanufacturing a single-use or single-patient-use medical device does not convert it into a reusable device. Instead, it becomes a remanufactured single-use or single-patient-use device, safe for use after undergoing remanufacturing. It must be remanufactured between uses.
Remanufactured Medical devices are subject to the same regulatory requirements as original devices. Medsalv remanufactured devices are marked as remanufactured by Medsalv on the device, to ensure stringent product traceability.
A Medsalv remanufactured single-use medical device holds an ARTG (Australia) or WAND Listing (New Zealand), the same as any other single-use device.
This is a separate listing to the original device, because Medsalv becomes the Manufacturer of Record for the remanufactured device.
Our procurement team is concerned that working with Medsalv might harm relationships with current suppliers and is reluctant to move forward because of this, despite your track record and the cost savings you offer. Why might this be the case?
Our programs have been successfully implemented in over 100 hospitals across Australasia, though we understand that some concerns can arise, often influenced by the established presence of incumbent suppliers.
Medsalv occasionally collaborates with Original Suppliers when there’s alignment in values, but our mission is to Change Healthcare For Good —a goal that sometimes challenges the existing landscape.
Long-standing contracts and supplier relationships can make procurement teams cautious about changing supply chains, even with clear benefits.
Medsalv addresses these concerns by providing thorough information and support, ensuring a smooth adjustment to your product mixture that offers cost savings, environmental and social benefits, and addresses your hospital-specific needs.
If your hospital is part of the public sector, these may amount to probity concerns.
Medsalv occasionally collaborates with Original Suppliers when there’s alignment in values, but our mission is to Change Healthcare For Good —a goal that sometimes challenges the existing landscape.
Long-standing contracts and supplier relationships can make procurement teams cautious about changing supply chains, even with clear benefits.
Medsalv addresses these concerns by providing thorough information and support, ensuring a smooth adjustment to your product mixture that offers cost savings, environmental and social benefits, and addresses your hospital-specific needs.
If your hospital is part of the public sector, these may amount to probity concerns.
I wouldn't mind having a look around a remanufacturing facility. Is this possible?
Absolutely!
We encourage customer visits for to provide transparency and allow stakeholders to see firsthand the quality and the standards maintained in our remanufacturing process, and meet the people who we're making an impact with through our social employment practcies.
Contact us to arrange a tour - Our Facilities are located in Christchurch (Canterbury, New Zealand) and Geelong (Victoria, Australia)
We encourage customer visits for to provide transparency and allow stakeholders to see firsthand the quality and the standards maintained in our remanufacturing process, and meet the people who we're making an impact with through our social employment practcies.
Contact us to arrange a tour - Our Facilities are located in Christchurch (Canterbury, New Zealand) and Geelong (Victoria, Australia)
What’s the environmental impact of remanufacturing compared to recycling or disposal?
Remanufacturing with Medsalv has a significantly lower environmental footprint than disposal or recycling, and how much depends on a number of factors including the device material composition and how far it needs to travel.
Compared to other Remanufacturers (or reprocessors): Based on currently available data, Medsalv’s remanufacturing processes in New Zealand generate 50-60% less emissions than comparable reprocessing processes from other manufacturers.
Compared to new products: By returning devices to a functional state, we reduce the demand for new products and the associated resources and emissions – all products we remanufacture are imported, so this is significant. Based on the same currently available data, Medsalv's processes generate 75% less emissions compared to manufacturing the predicate device.
Compared to new products and recycling: Recycling, while better than disposal, still consumes energy and typically doesn’t recover the full material value of the product. Remanufacturing keeps products in use longer, contributing to a circular economy and reducing waste - further up the waste hierarchy.
Compared to other Remanufacturers (or reprocessors): Based on currently available data, Medsalv’s remanufacturing processes in New Zealand generate 50-60% less emissions than comparable reprocessing processes from other manufacturers.
Compared to new products: By returning devices to a functional state, we reduce the demand for new products and the associated resources and emissions – all products we remanufacture are imported, so this is significant. Based on the same currently available data, Medsalv's processes generate 75% less emissions compared to manufacturing the predicate device.
Compared to new products and recycling: Recycling, while better than disposal, still consumes energy and typically doesn’t recover the full material value of the product. Remanufacturing keeps products in use longer, contributing to a circular economy and reducing waste - further up the waste hierarchy.
I'm an Infection Preventionist, how can I contribute to a successful program?
Collections are the foundation of a successful programme. Any infection control concerns related to New Product use are fully addressed through compliance with TGA requirements for ARTG registration, ISO 13485:2016 standards, and other relevant guidelines.
Safe collections are crucial. While a well-established infection control team may not need extensive involvement, it’s important for the IPC team to be engaged at key stages to ensure our collection criteria align smoothly with hospital IPC processes.
Our criteria are standardised, but we recognise that hospitals manage waste differently. To support this, we align our collection criteria with hospital-specific terminology or seek IPC endorsement of our processes.
This approach ensures simplicity and reduces the risk of confusion.
We provide comprehensive collection data and proactively identify any issues, helping maintain safe, effective and compliant processes throughout.
Safe collections are crucial. While a well-established infection control team may not need extensive involvement, it’s important for the IPC team to be engaged at key stages to ensure our collection criteria align smoothly with hospital IPC processes.
Our criteria are standardised, but we recognise that hospitals manage waste differently. To support this, we align our collection criteria with hospital-specific terminology or seek IPC endorsement of our processes.
This approach ensures simplicity and reduces the risk of confusion.
We provide comprehensive collection data and proactively identify any issues, helping maintain safe, effective and compliant processes throughout.
How can I trust a third-party remanufacturer who didn’t originally make the devices to do this safely? Wouldn’t it be better to work with the OEM and their 'reprocessing'?
That’s a fair question. Currently, no OEMs are purely dedicated to remanufacturing; any reprocessing or remanufacturing operations associated with OEMs were acquired rather than developed in-house.
Evidence suggests these acquisitions may have been made to protect market share rather than drive sustainability.
Both manufacturing and remanufacturing are regulated as manufacturing by the TGA, with strict quality standards in place. However, while the end products are the same, the processes to achieve them are fundamentally different. Simply put, the ability to manufacture a device does not equate to the ability to remanufacture it—and certainly doesn’t imply it can’t be safely remanufactured by others.
When a product is labelled as single-use, it typically means the manufacturer hasn’t invested the resources to validate it for safe reuse or designate it as reusable. This does not prevent a qualified organisation, like Medsalv, from undertaking this validation. As a third-party remanufacturer, Medsalv adheres to stringent regulatory standards, including ISO 13485:2016, ensuring each remanufactured device is safe, fully functional, and meets or exceeds the original quality benchmarks.
Unlike OEMs, Medsalv generates no revenue from the sale of original single-use devices, allowing us to focus solely on providing high-quality, safe, and sustainable remanufactured products.
While some OEMs may offer limited reprocessing options, their focus may lie in profitability, or selling original devices. In contrast, Medsalv’s mission is fully dedicated to delivering tailored, cost-effective solutions for hospitals without conflicting incentives.
By choosing Medsalv, you partner with an organisation trusted by over 100 hospitals across Australasia, committed to transforming healthcare with a focus on safety, compliance, and long-term sustainability.
Evidence suggests these acquisitions may have been made to protect market share rather than drive sustainability.
Both manufacturing and remanufacturing are regulated as manufacturing by the TGA, with strict quality standards in place. However, while the end products are the same, the processes to achieve them are fundamentally different. Simply put, the ability to manufacture a device does not equate to the ability to remanufacture it—and certainly doesn’t imply it can’t be safely remanufactured by others.
When a product is labelled as single-use, it typically means the manufacturer hasn’t invested the resources to validate it for safe reuse or designate it as reusable. This does not prevent a qualified organisation, like Medsalv, from undertaking this validation. As a third-party remanufacturer, Medsalv adheres to stringent regulatory standards, including ISO 13485:2016, ensuring each remanufactured device is safe, fully functional, and meets or exceeds the original quality benchmarks.
Unlike OEMs, Medsalv generates no revenue from the sale of original single-use devices, allowing us to focus solely on providing high-quality, safe, and sustainable remanufactured products.
While some OEMs may offer limited reprocessing options, their focus may lie in profitability, or selling original devices. In contrast, Medsalv’s mission is fully dedicated to delivering tailored, cost-effective solutions for hospitals without conflicting incentives.
By choosing Medsalv, you partner with an organisation trusted by over 100 hospitals across Australasia, committed to transforming healthcare with a focus on safety, compliance, and long-term sustainability.
Do I need manufacturer approval for me to use Medsalv remanufactured products? What about if there’s a pump?
No.
Original manufacturers or distributors are unable to endorse the efficacy of Medsalv’s products or processes, as our remanufacturing methods are proprietary (And Medsalv's technical accreditations and certifcations far outstrip most suppliers in the Australian market).
Even if they could, it’s unlikely they would endorse Medsalv products, as doing so could impact their own revenue.
Additionally, manufacturers that restrict hospital access to capital equipment they have placed may be raising serious competition law concerns.
We recommend that hospitals consider purchasing or renting capital equipment at a fair market rate to promote competition in the capital equipment market, optimise healthcare spending, and get a better deal.
If your hospital feels it may be overpaying for capital equipment, talk to us about strategies to manage this more effectively.
Original manufacturers or distributors are unable to endorse the efficacy of Medsalv’s products or processes, as our remanufacturing methods are proprietary (And Medsalv's technical accreditations and certifcations far outstrip most suppliers in the Australian market).
Even if they could, it’s unlikely they would endorse Medsalv products, as doing so could impact their own revenue.
Additionally, manufacturers that restrict hospital access to capital equipment they have placed may be raising serious competition law concerns.
We recommend that hospitals consider purchasing or renting capital equipment at a fair market rate to promote competition in the capital equipment market, optimise healthcare spending, and get a better deal.
If your hospital feels it may be overpaying for capital equipment, talk to us about strategies to manage this more effectively.
But my supplier says they have made parts of the product unable to be remanufactured?
Unfortunately, this (forced obsolescence) does happen, and there are a number of instances of the same behaviour happening.
Just put a common yellow single-use tourniquet in a normal cleaning process for a reusable, and you’ll see it happen.
Luckily we have a smart team who develop processes that work around these types of wasteful tactics while retaining the safety and efficacy of the remanufacturing process.
If your supplier has deliberately designed a product to prevent it from being
remanufactured you should find another supplier.
Talk to us about your options.
Just put a common yellow single-use tourniquet in a normal cleaning process for a reusable, and you’ll see it happen.
Luckily we have a smart team who develop processes that work around these types of wasteful tactics while retaining the safety and efficacy of the remanufacturing process.
If your supplier has deliberately designed a product to prevent it from being
remanufactured you should find another supplier.
Talk to us about your options.
How do I get started? And how much work is involved?
Getting started is simple! Just click the "Get on Board" link above to begin.
We have a well-defined process that we’ll guide your hospital through, enabling you to set up collections as fast as a week, with buyback programs to follow.
The fastest total implementation we've completed was under a week, but we're there to guide you through all the internal approvals you may need - large hospitals may take longer.
Medsalv’s programs are designed to operate seamlessly across Australia and New Zealand and can be implemented remotely.
The more details you provide when filling out our form, the easier it will be for us to tailor the program to meet your hospital’s needs.
We have a well-defined process that we’ll guide your hospital through, enabling you to set up collections as fast as a week, with buyback programs to follow.
The fastest total implementation we've completed was under a week, but we're there to guide you through all the internal approvals you may need - large hospitals may take longer.
Medsalv’s programs are designed to operate seamlessly across Australia and New Zealand and can be implemented remotely.
The more details you provide when filling out our form, the easier it will be for us to tailor the program to meet your hospital’s needs.
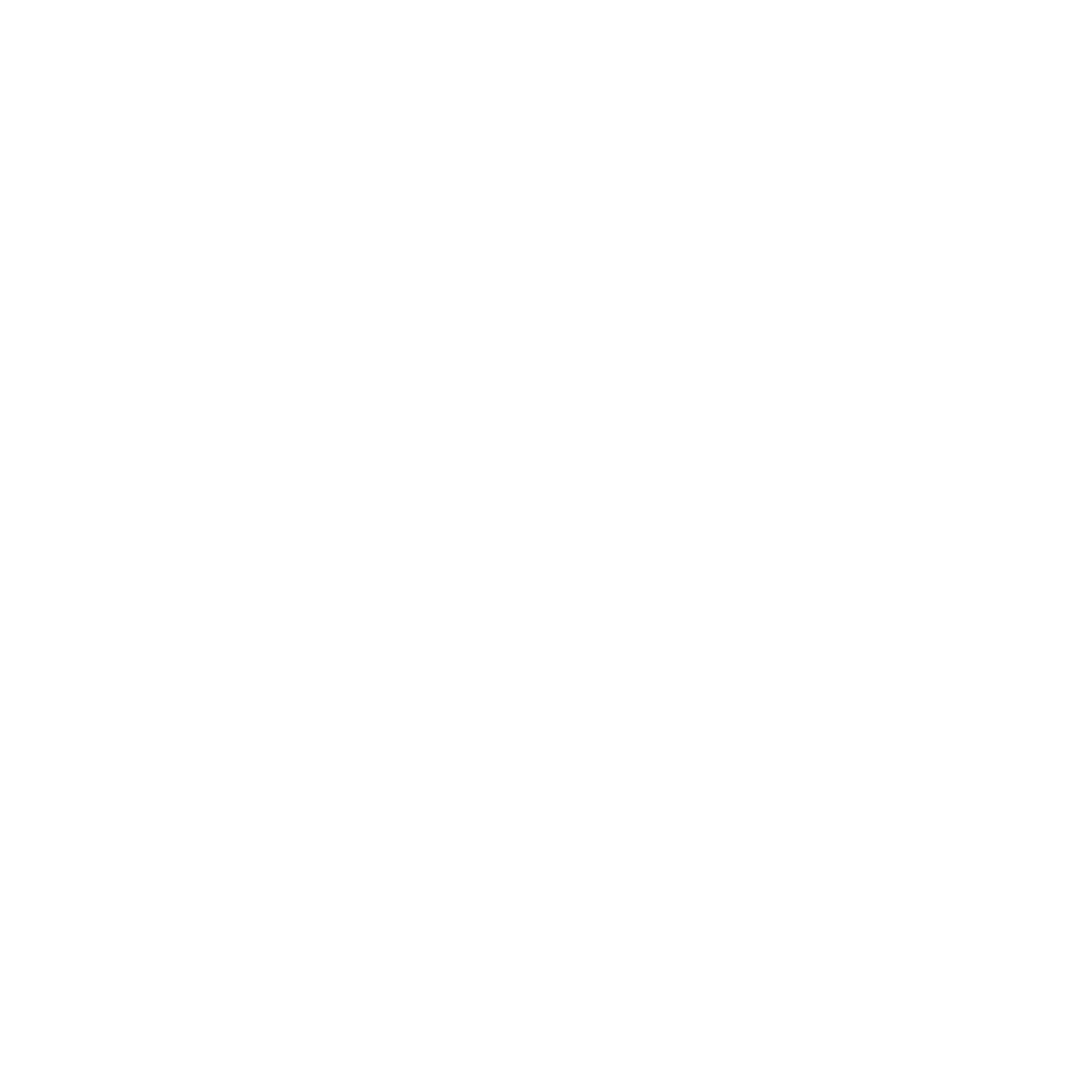
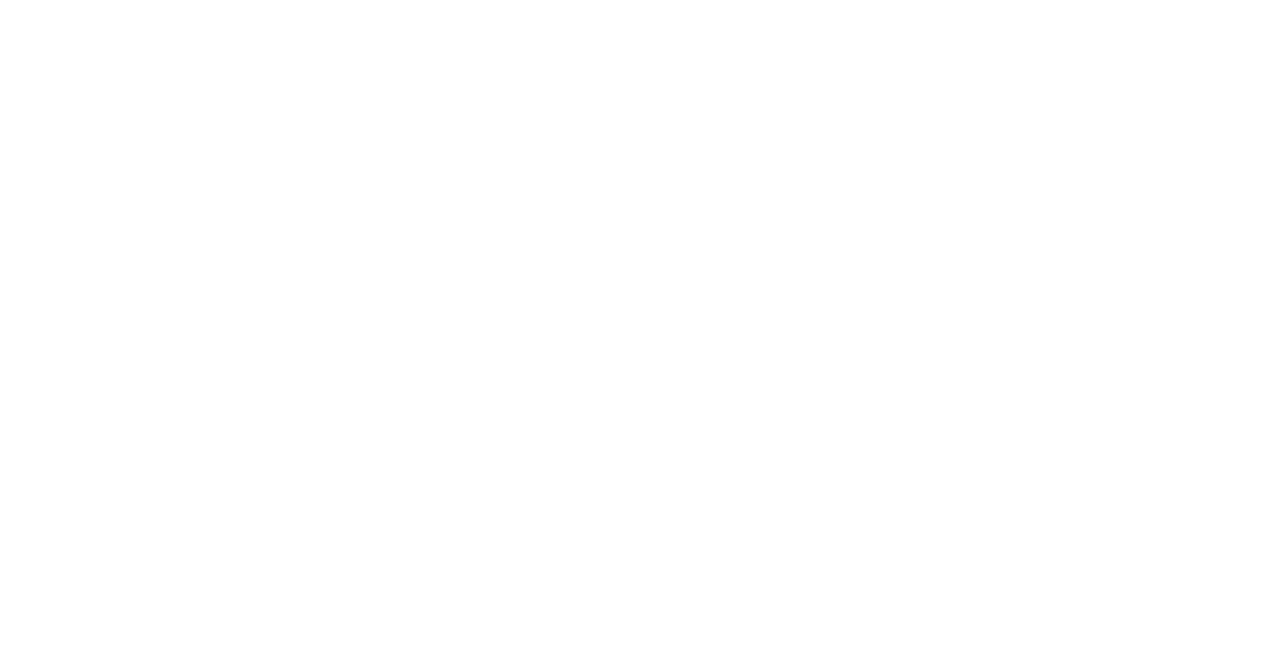
.webp)
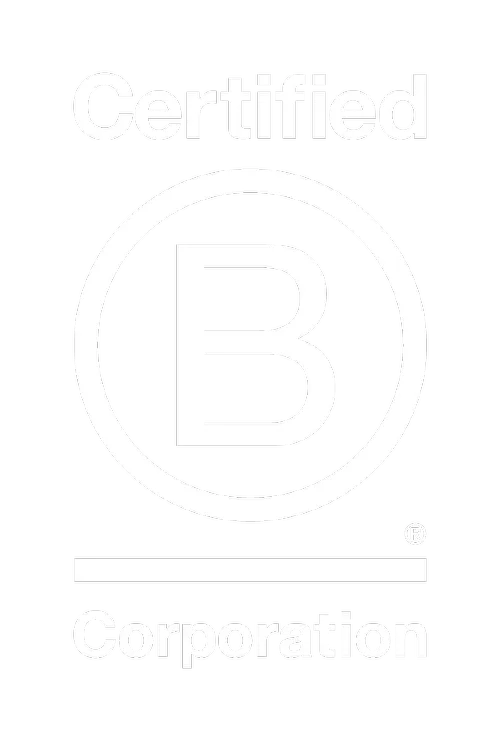
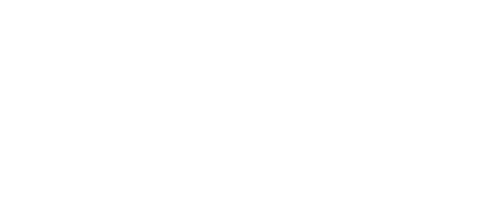
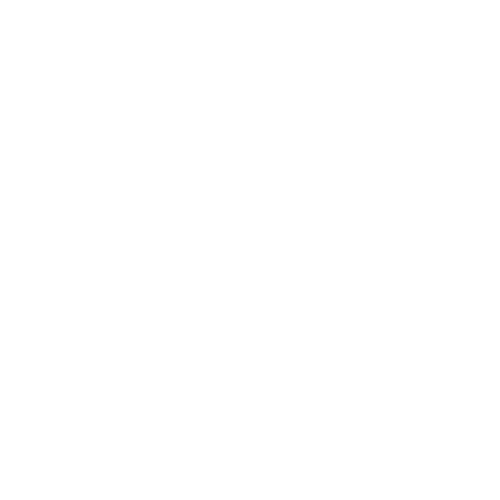
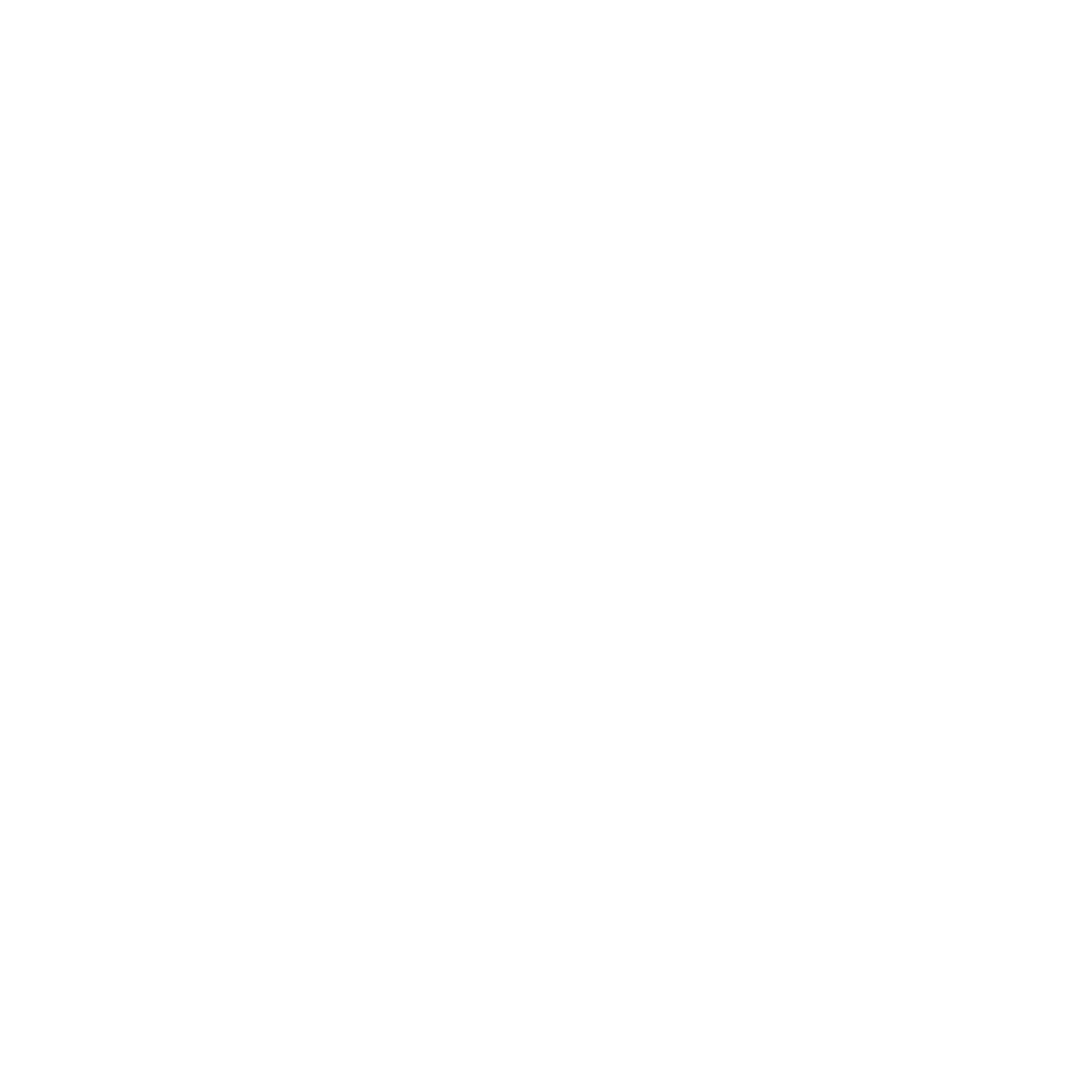
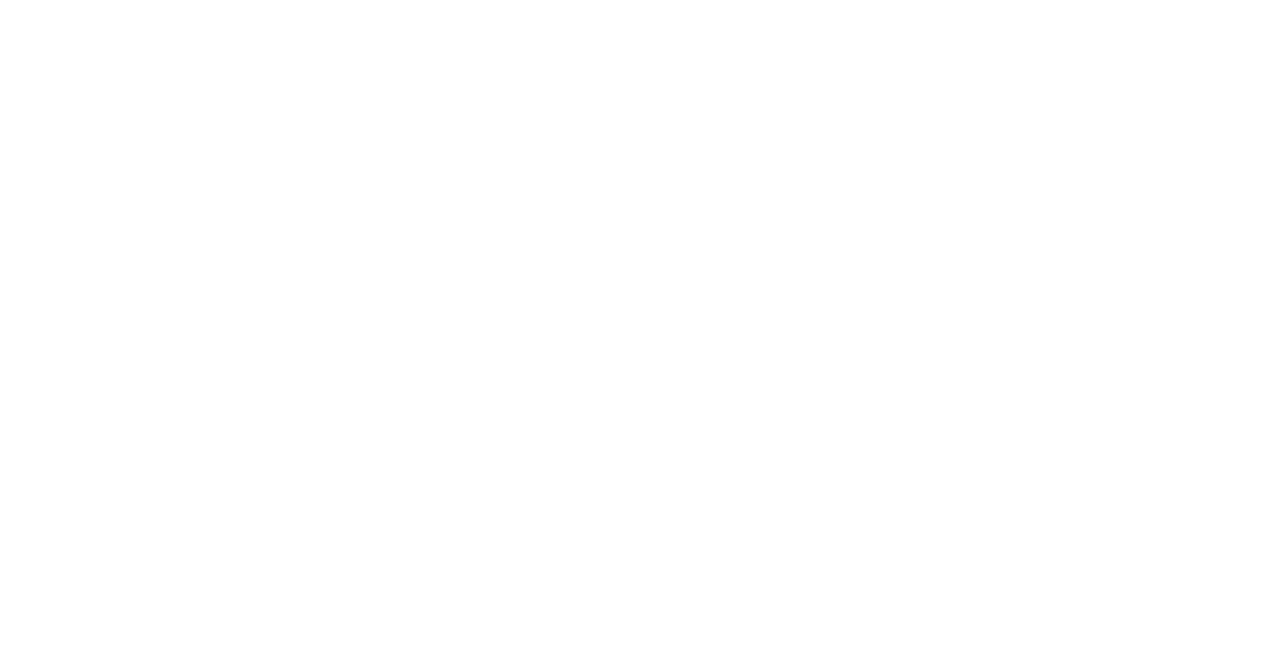
.webp)
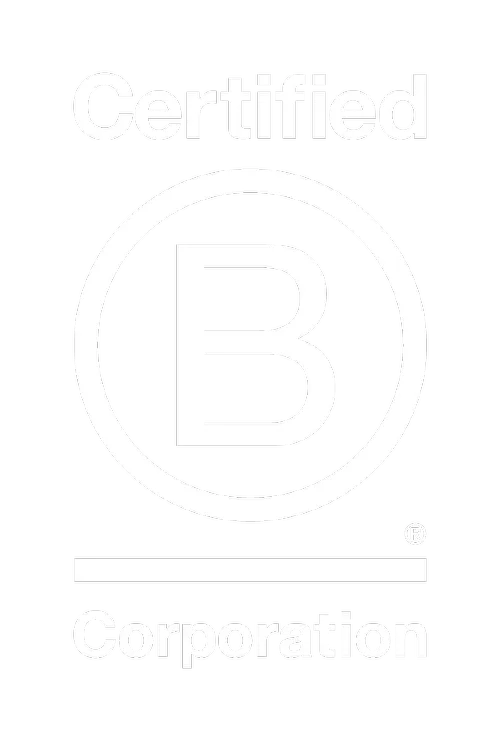
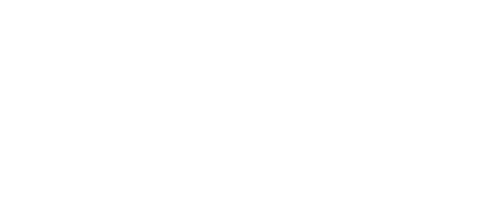
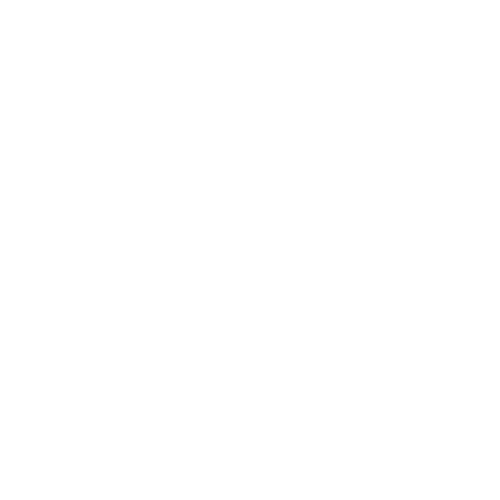
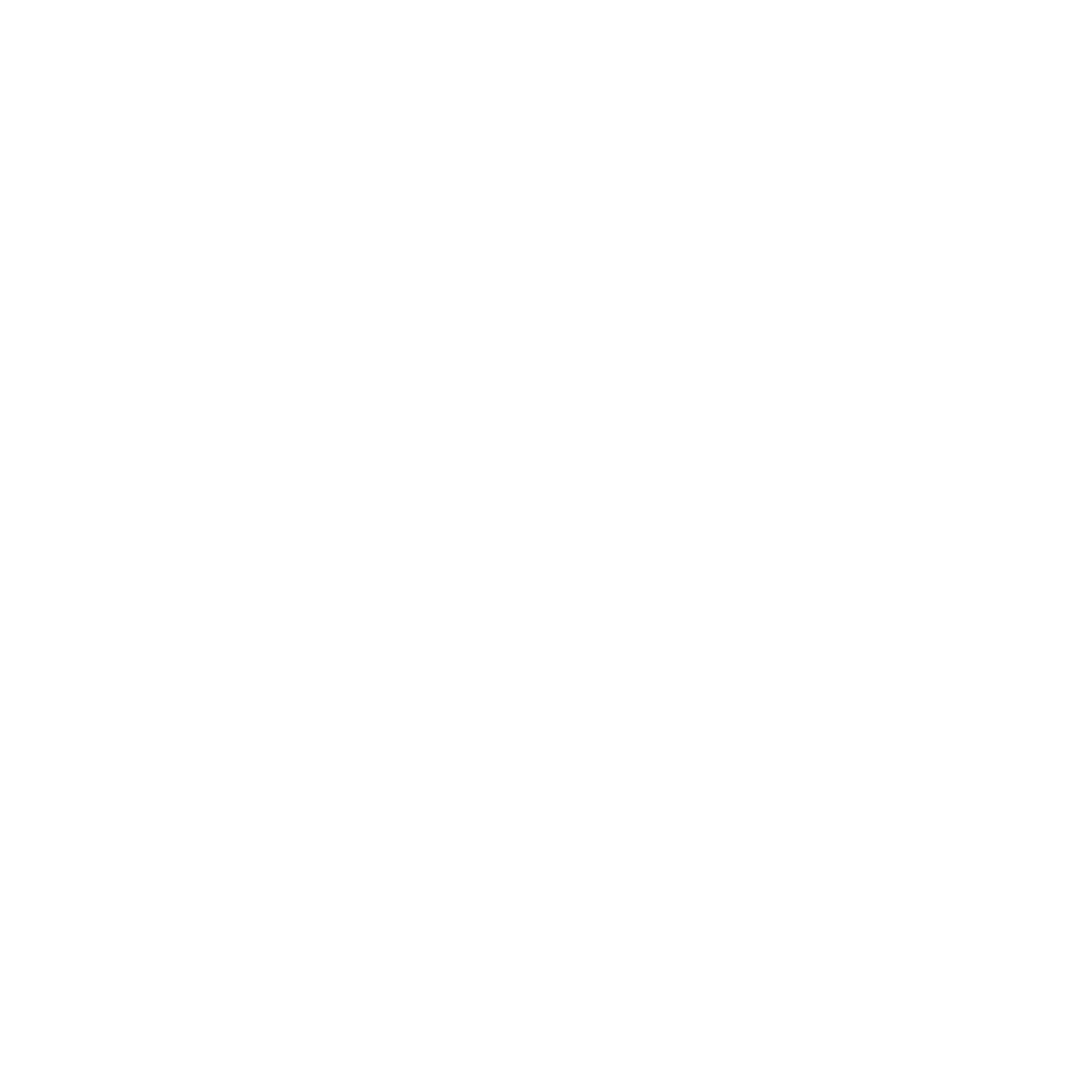
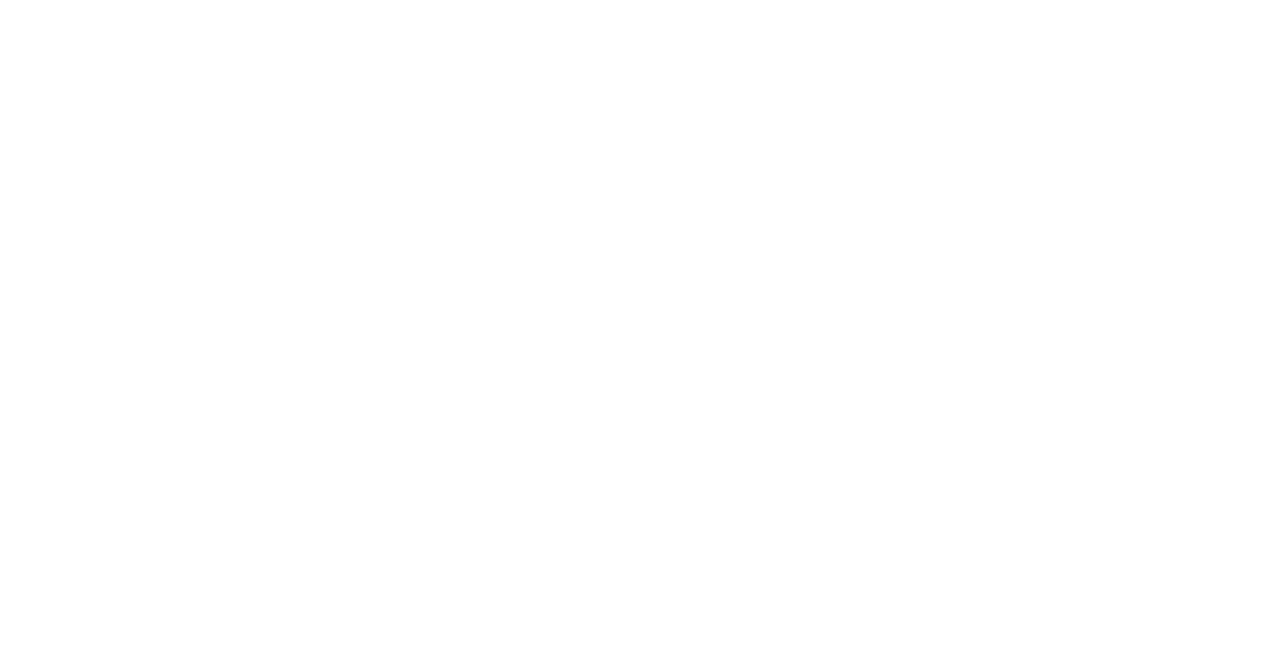
.webp)
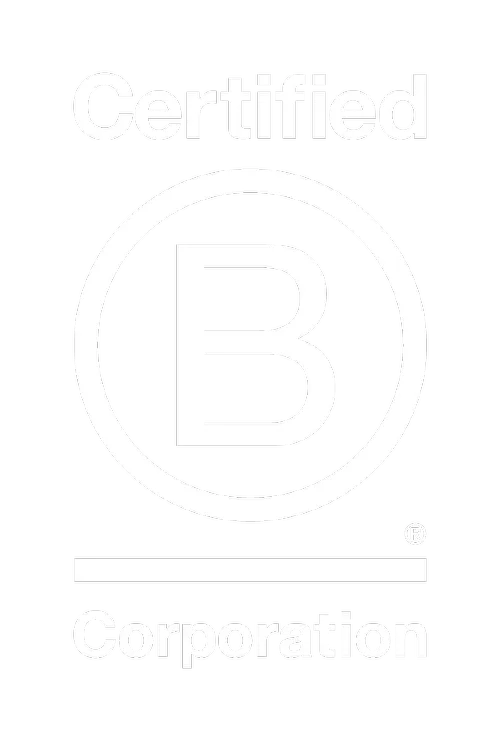
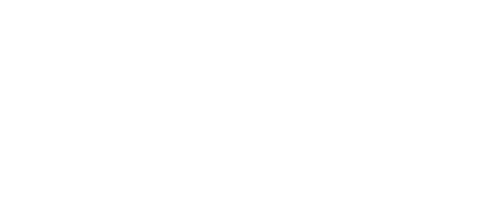
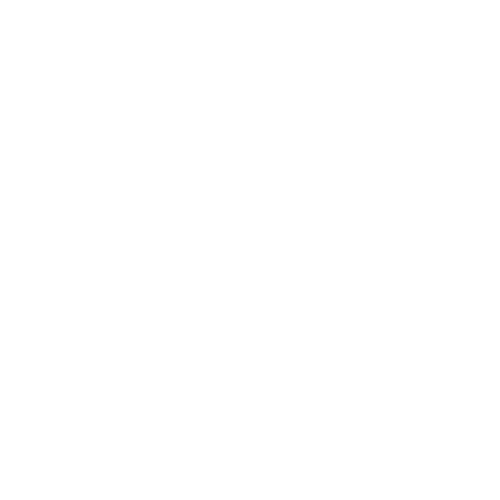
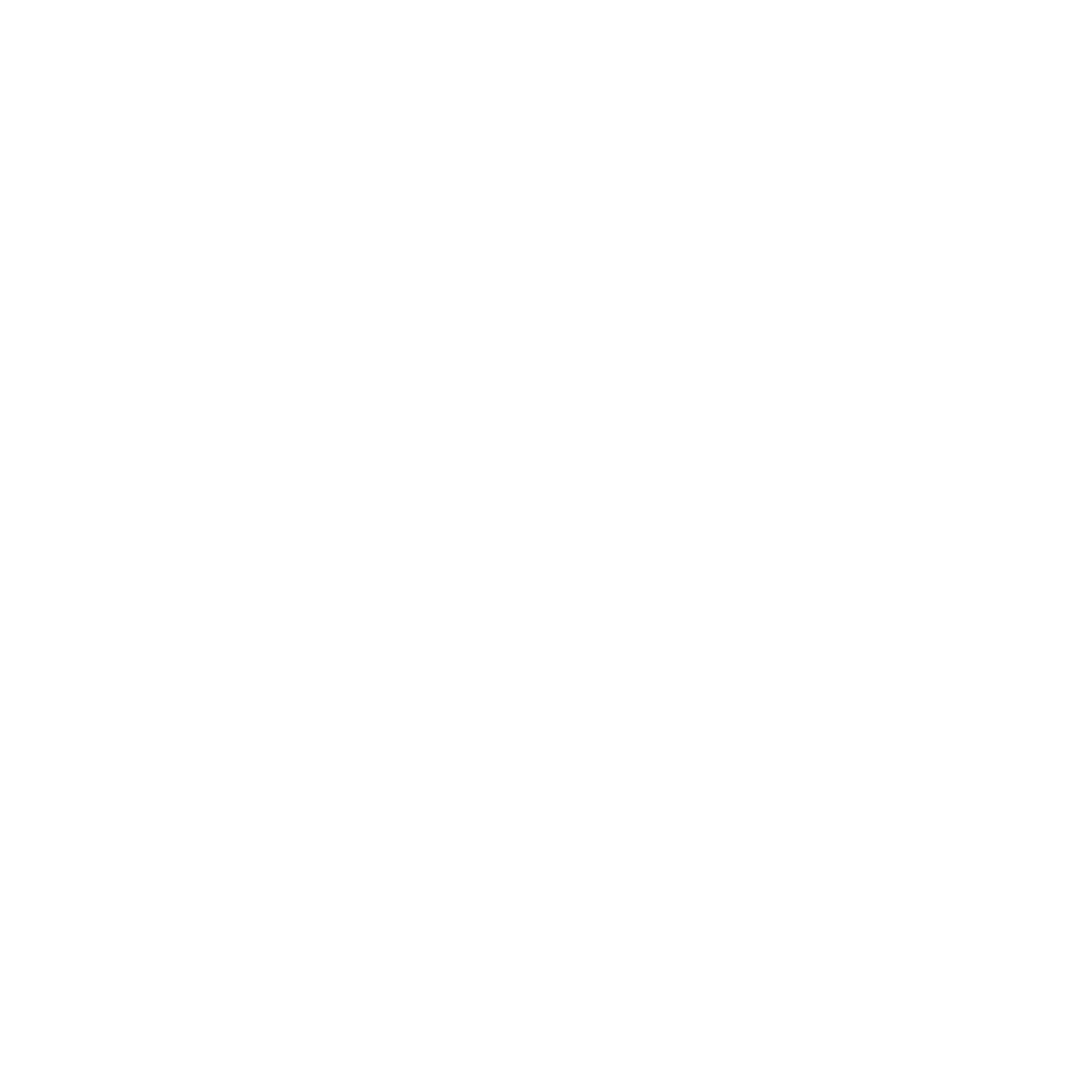
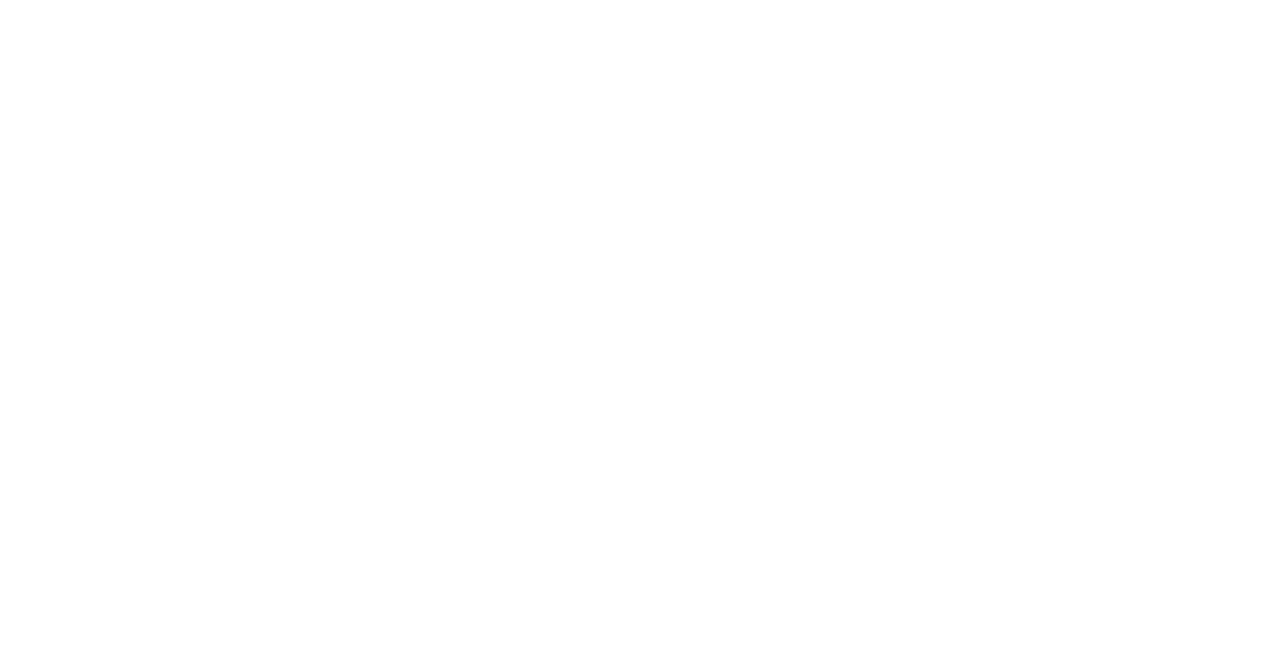
.webp)
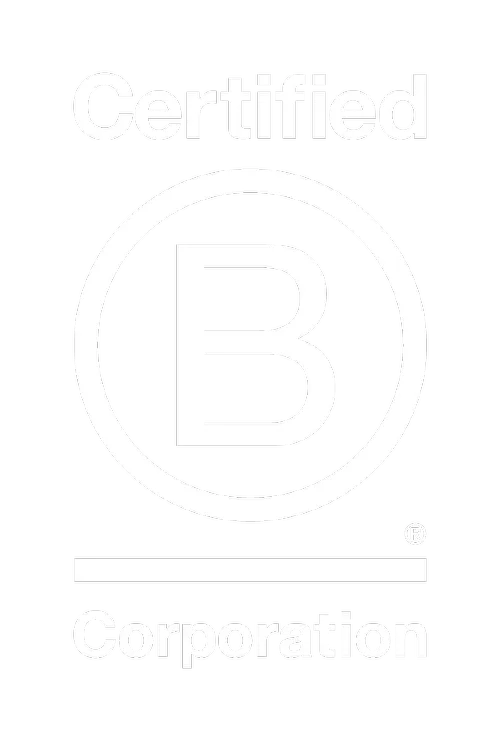
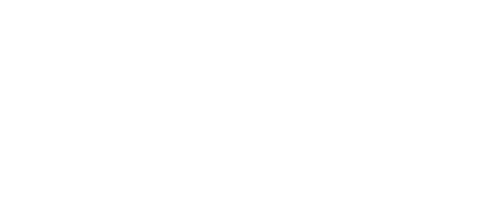
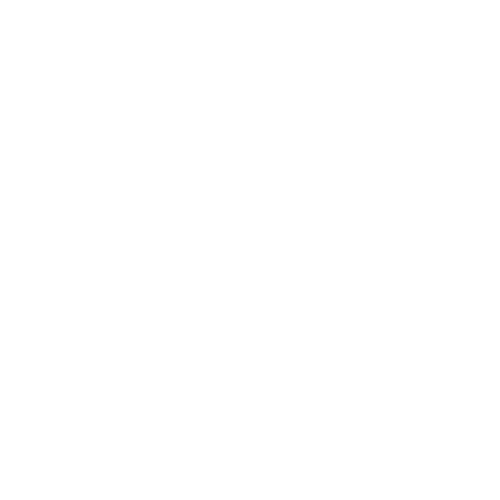
Healthcare shouldn't harm the planet.
Help us to change healthcare, for good.
Book a collection with us today.
Make your impact positive