From waste to reuse
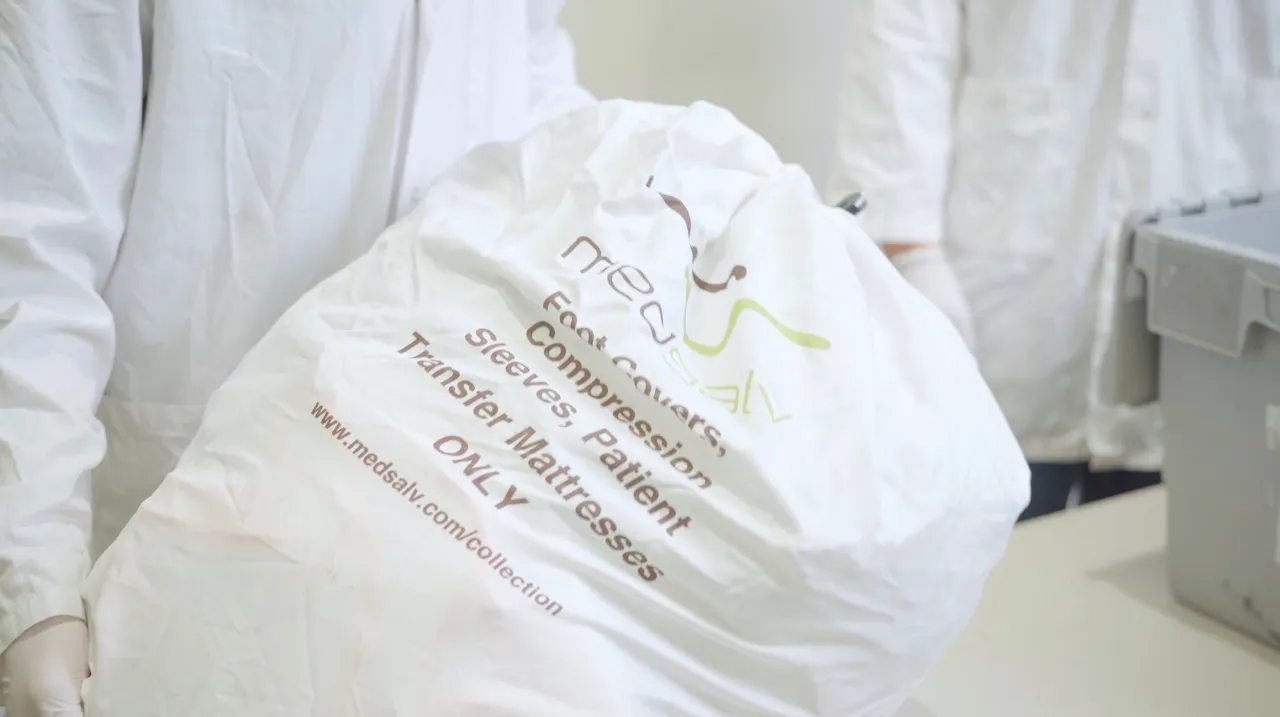
Medsalv's remanufacturing process gives new life to products that were previously sent to landfills after just one use.
From our simple online collection form to our unique remanufacturing facility, our detailed processes close the loop on sustainability and deliver remanufactured products that are equivalent to or better than brand new devices.
We’re ending the “make, waste, repeat” model.
- Cleans and disinfects products for safe reuse
- Doesn’t use a harsh sterilisation process
- Is non-toxic to the environment
- Uses reusable equipment for transport
- Is locally operated to minimise shipping and support local communities
- Employs people with barriers to employment
Hospital's collect their used devices. In urban areas Medsalv staff then regularly pick these up. Rural hospitals use a simple online portal to notify us when their collection bags are full.
We coordinate the delivery of the devices to our facility where they are separated and sorted by type, size, and condition. Each is marked with a Medsalv-branded Unique Device Identifier (UDI) for individual tracking.
The heart of the process lies in our proprietary cleaning and remanufacturing facility. The digitally tracked cleaning, retesting, labelling and packaging system puts each individual remanufactured device through a total of nine inspections.
These rigorous processes guarantee a patient experience that matches that of brand new devices - at up to 60% off the cost of a new device.
Final inspections and testing equipment ensure functionality and cleanliness before devices are packaged. With clear labels and instructions, clinical staff can easily distinguish between sizes and identify the device as Medsalv remanufactured.
The journey comes full circle with devices returned to the hospital in our reusable packaging. Our stackable, reusable cartons are used repeatedly to collect and deliver devices and close the loop on sustainability.
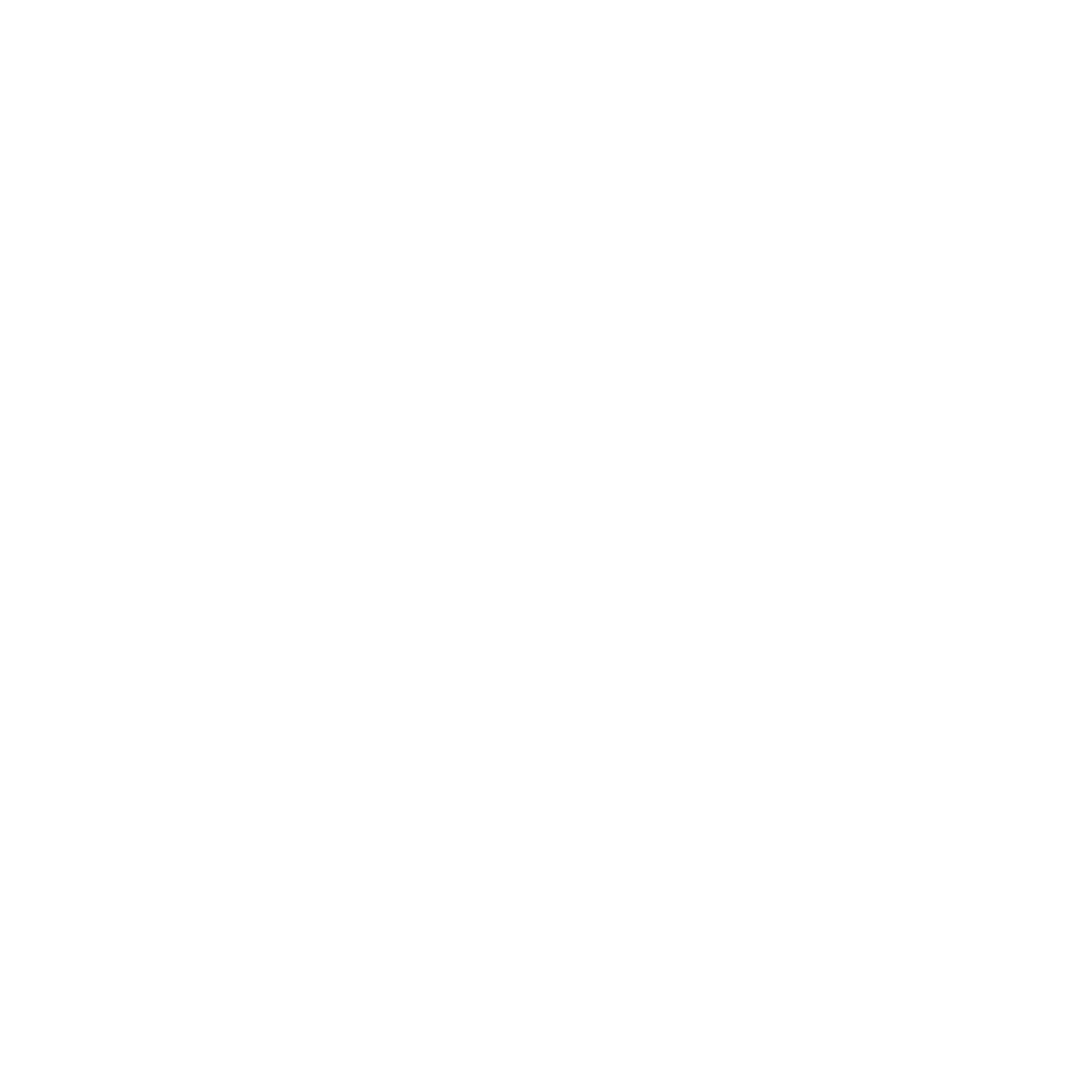
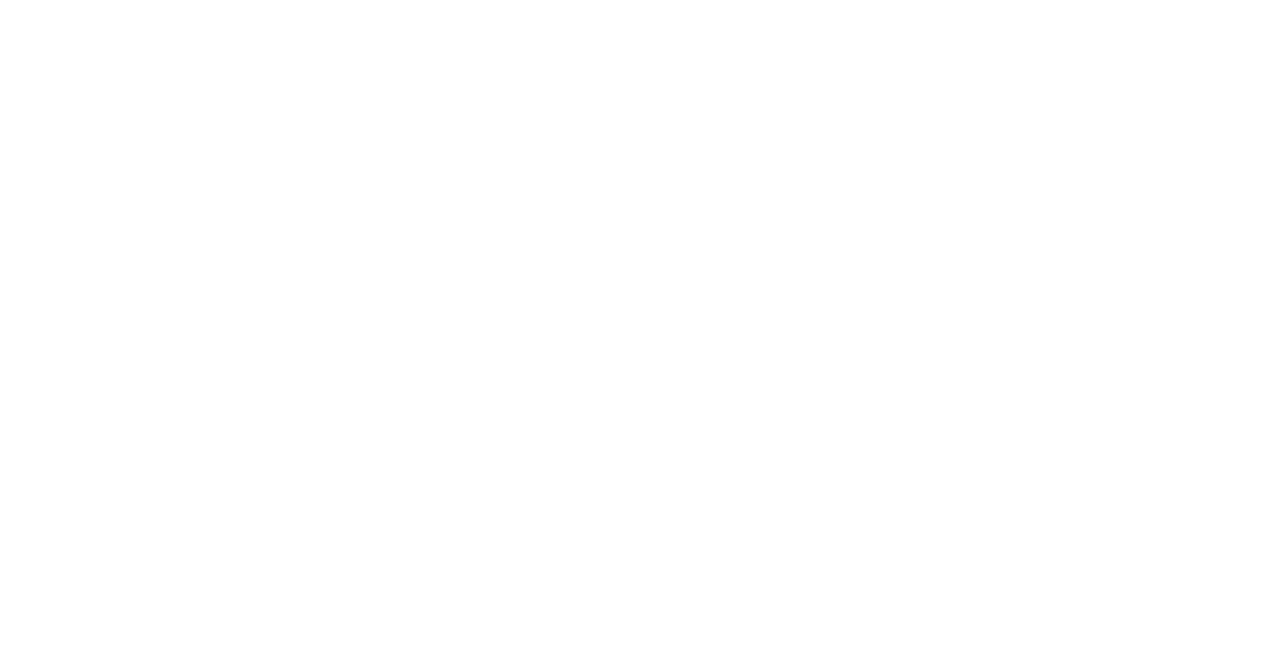
.webp)
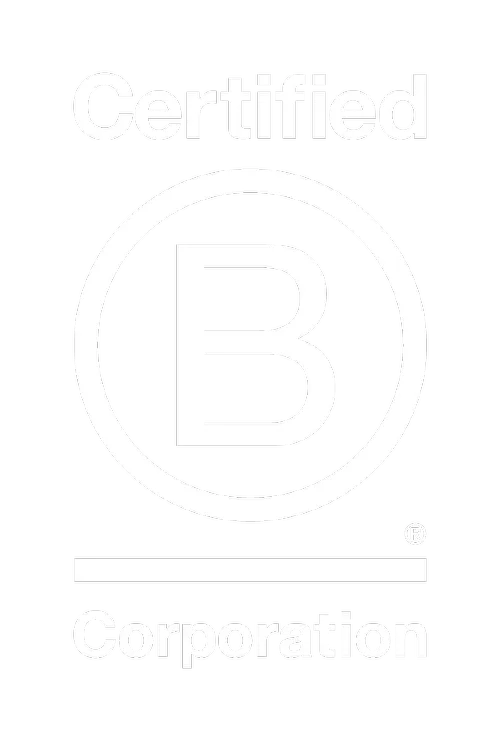
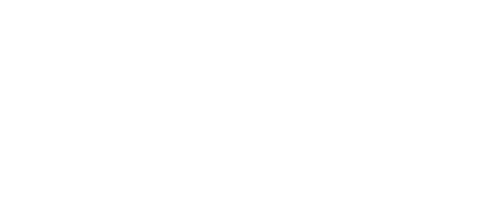
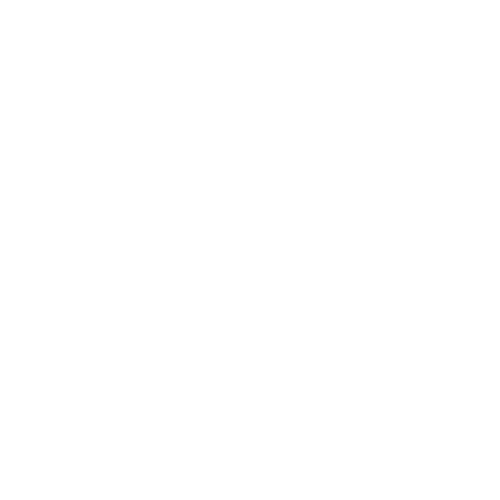
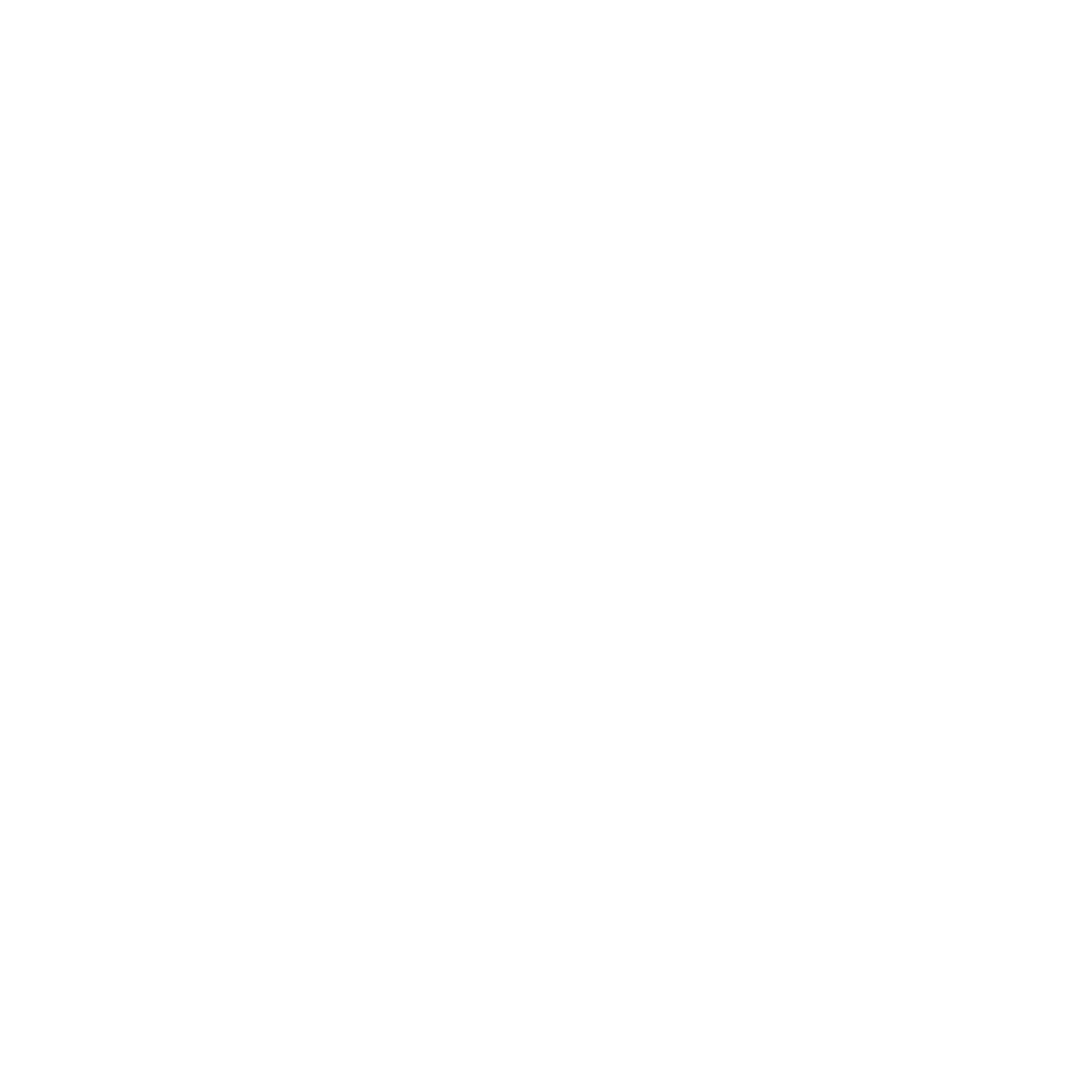
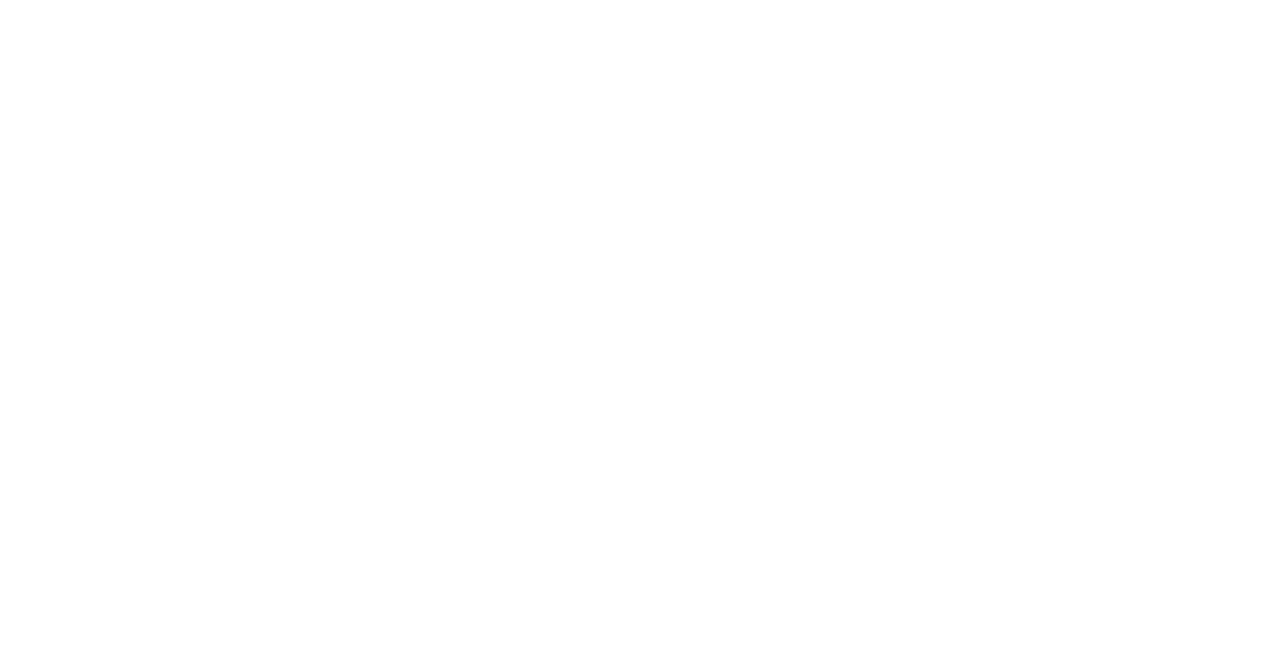
.webp)
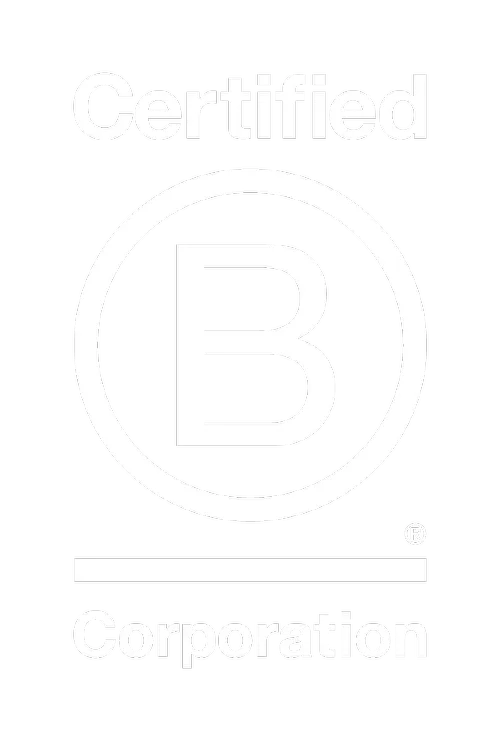
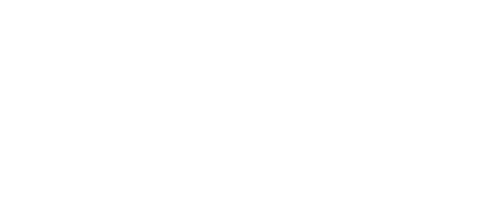
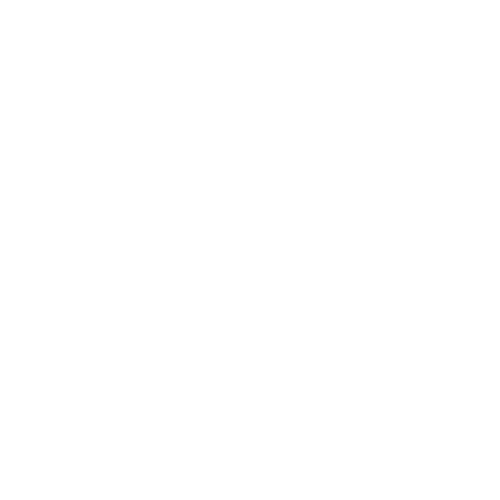
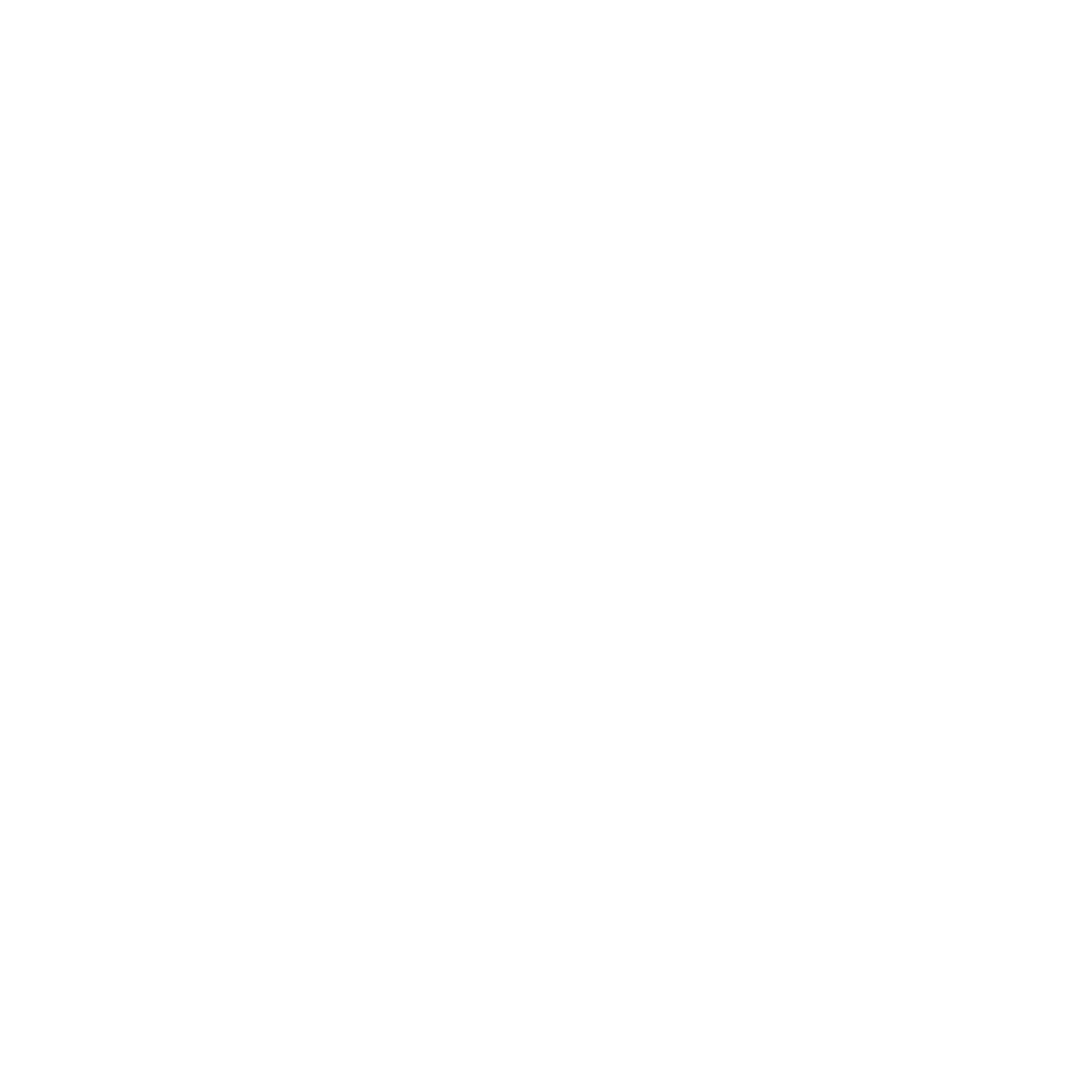
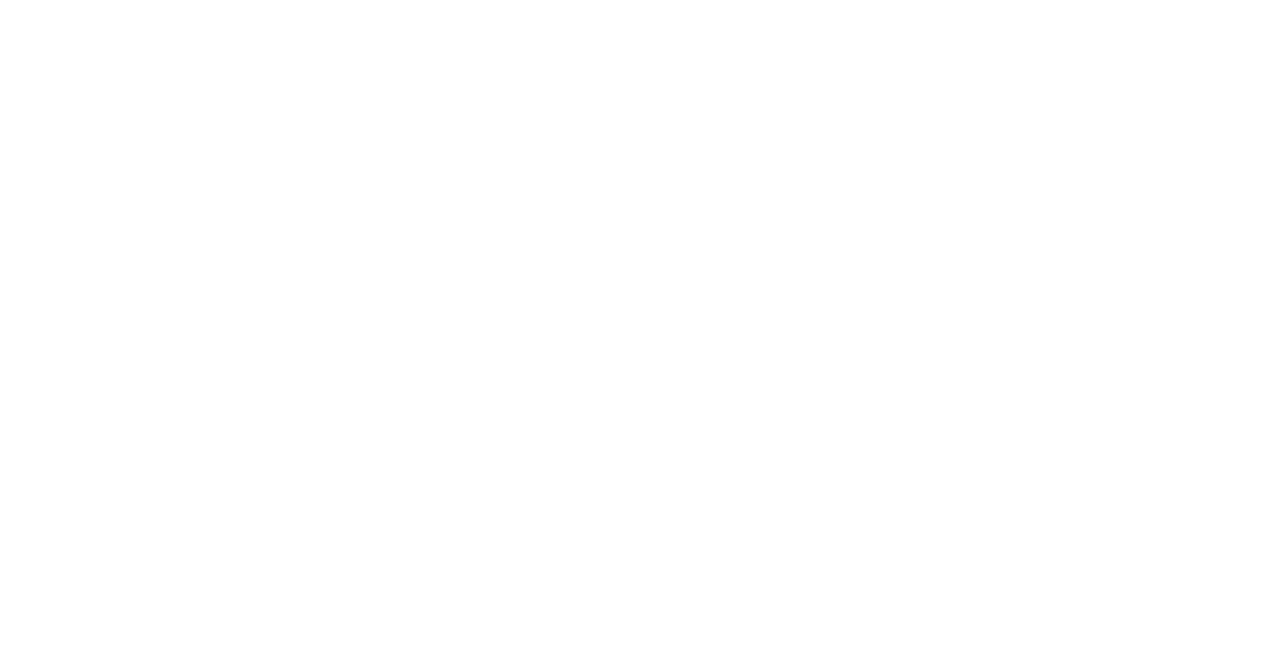
.webp)
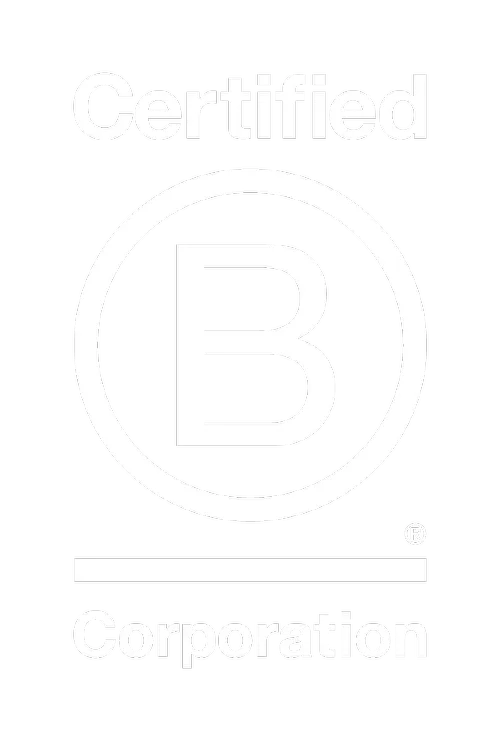
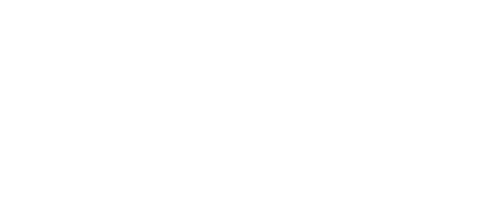
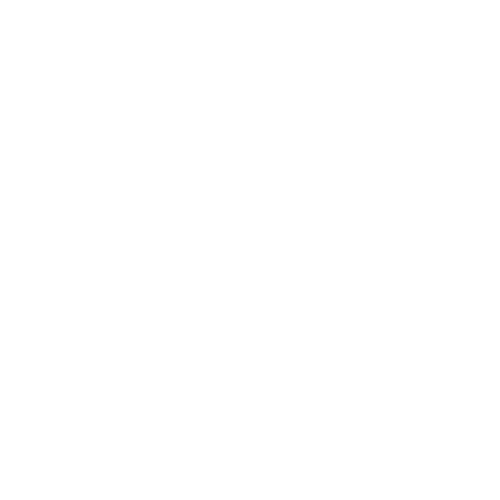
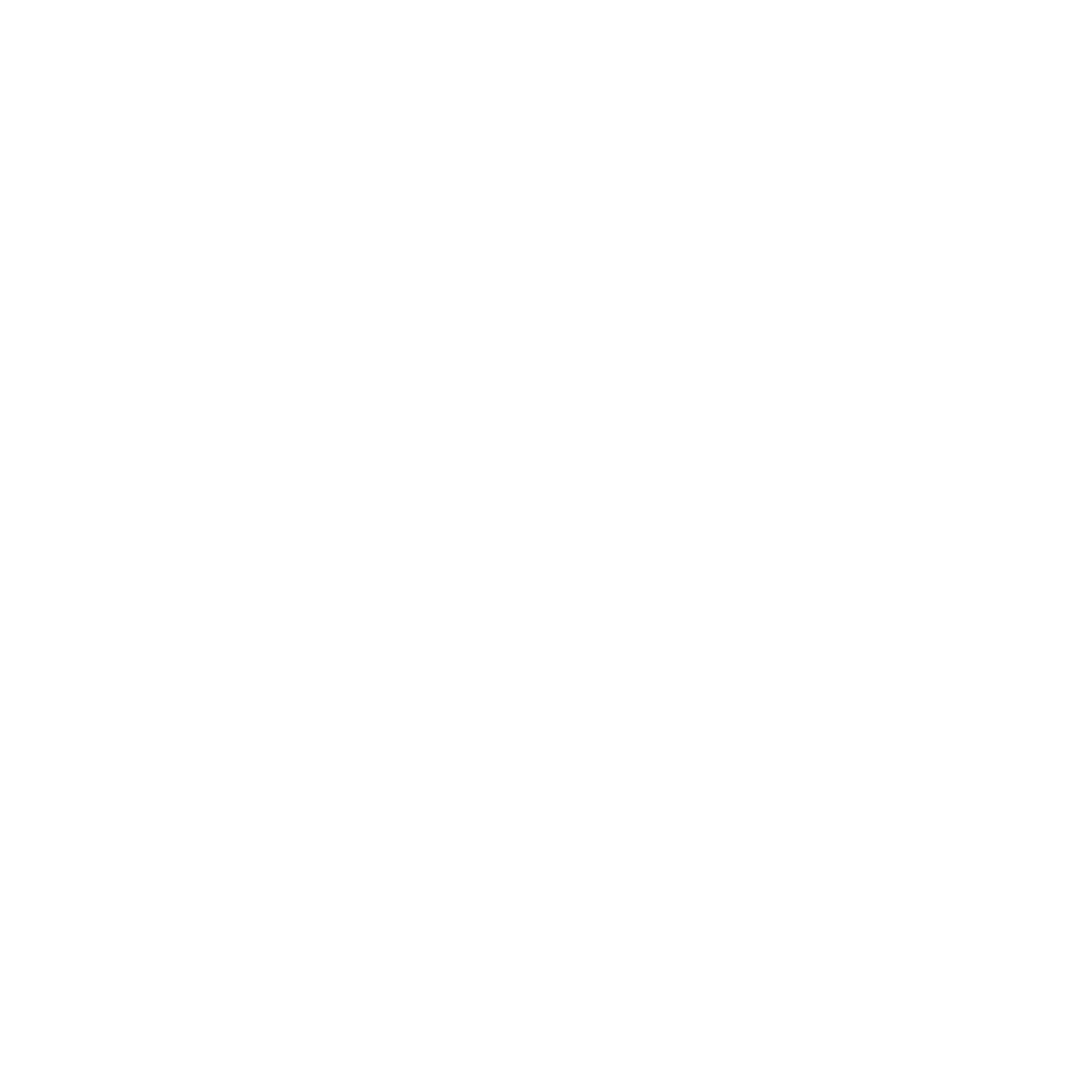
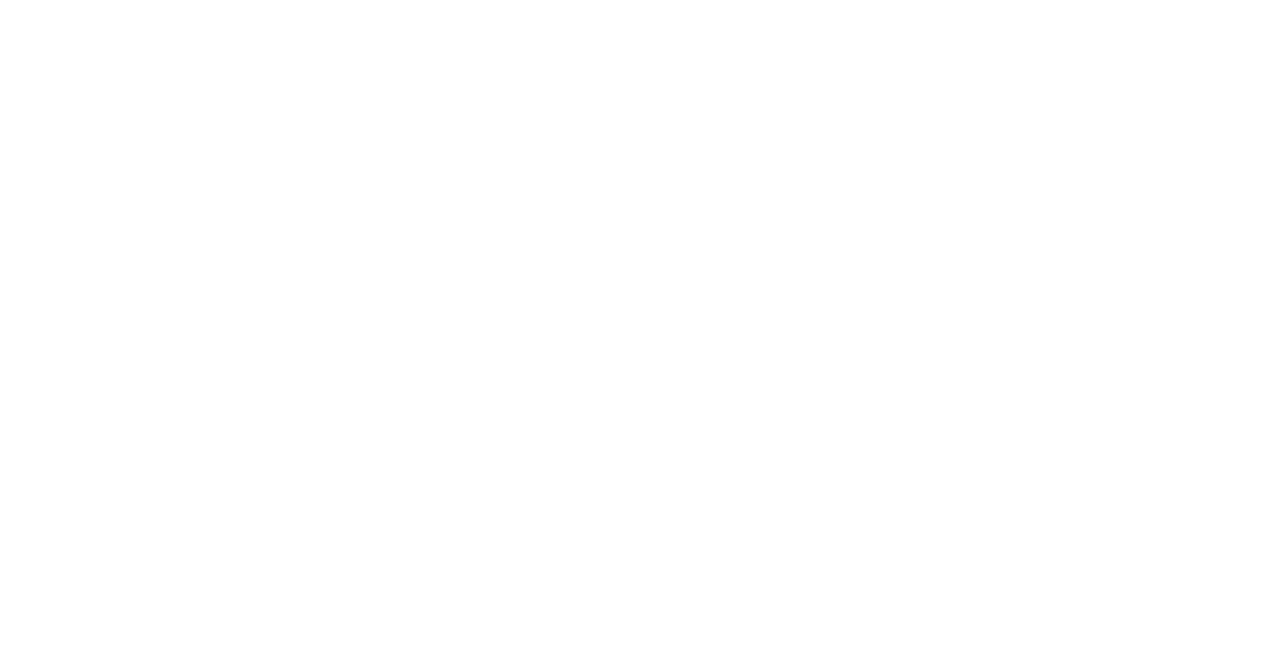
.webp)
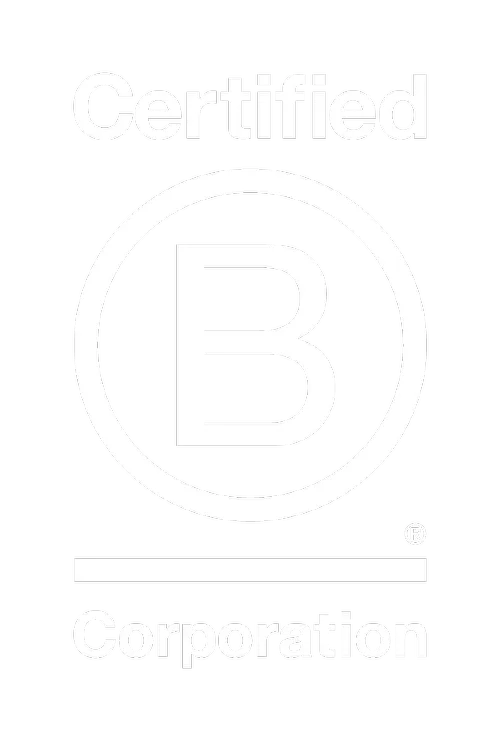
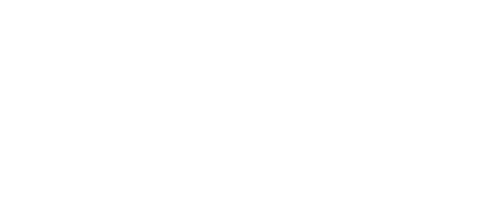
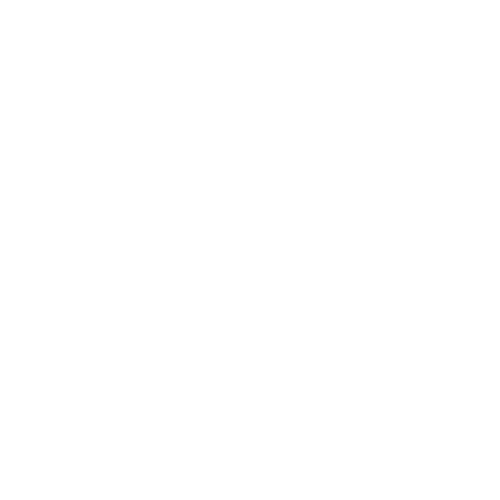